Retail Fleet In Focus: Embedding returns within the e-commerce offer
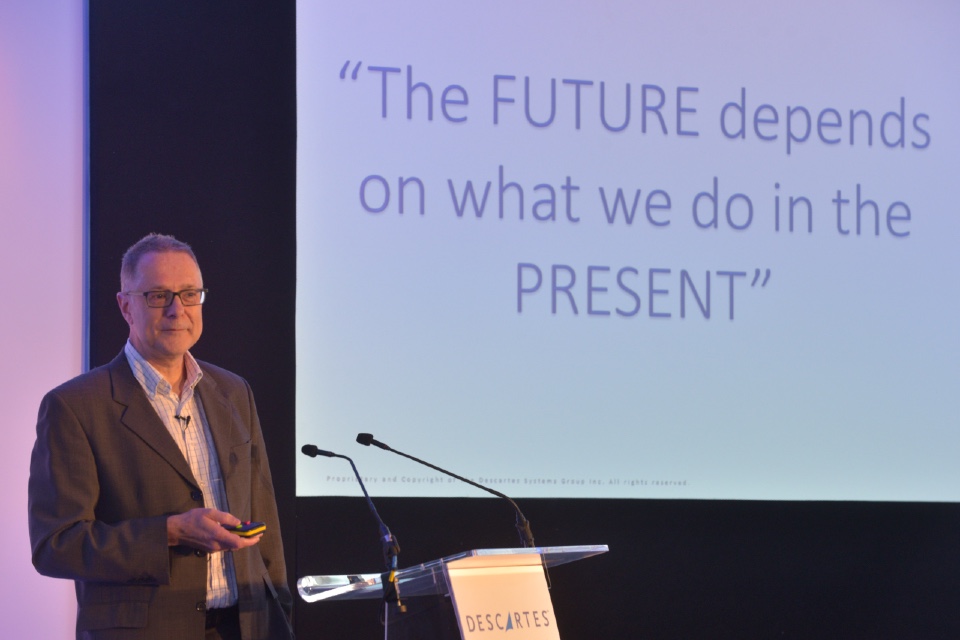
With a challenging 12 months ahead predicted to bring higher prices, retailers need to make radical changes to reduce costs and safeguard consumer loyalty and spending. Andrew Tavener, Head of Marketing at Descartes explores the opportunity to add returns collections to existing delivery schedules and the implications for cost control, reduced empty miles and customer experience… Spotlight on […]
The digital dispatcher has arrived – Here’s what that means for logistics
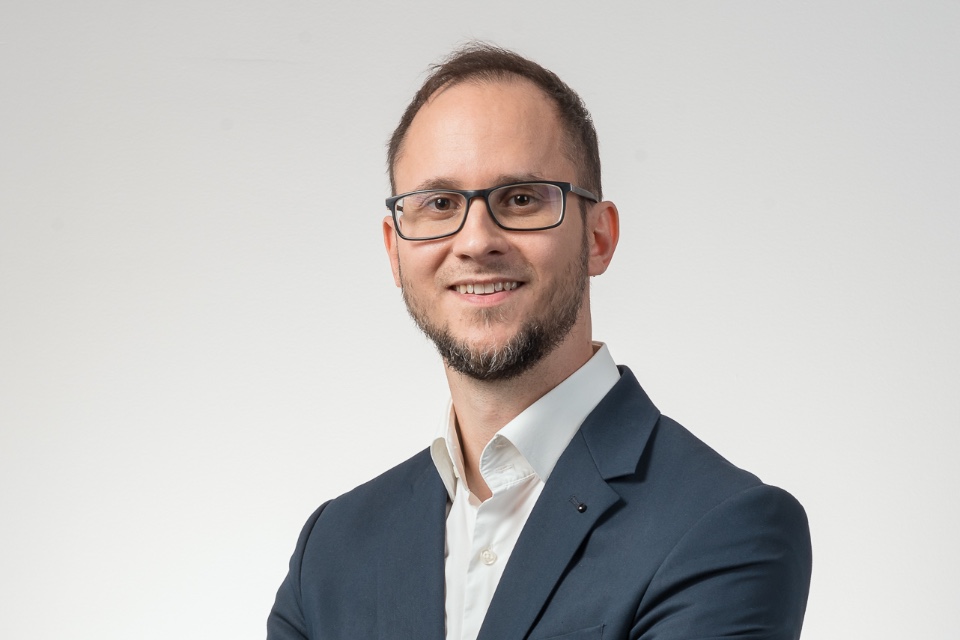
By András Kovács (pictured), Director of Fleet Products at Transporeon, A Trimble Company In the long-haul full truckload (FTL)L industry, dispatchers have traditionally relied on manual processes and years of experience to navigate a complex regulatory landscape, fluctuating fuel prices and evolving customer demands. While functional, this approach is far from optimal, putting pressure on dispatchers and leading to […]
eCMR: If not now, then when?
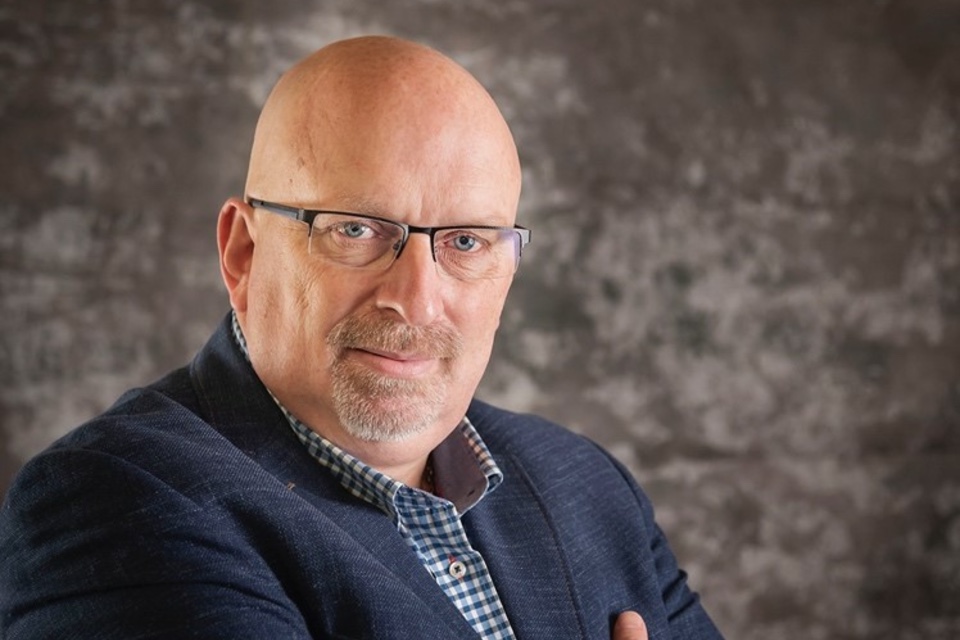
By Gerry Daalhuisen (pictured), Product Unit Lead Dock Scheduling & Yard Management at Transporeon, A Trimble Company There have been several unexpected pit stops on the road to eliminating paper-based processes in logistics. But, is paper finally set to be a thing of the past? 2024 marks 13 years since the official launch of the eCMR protocol […]
Data data data – The key for logistics and transportation businesses to meet their sustainability goals in 2024
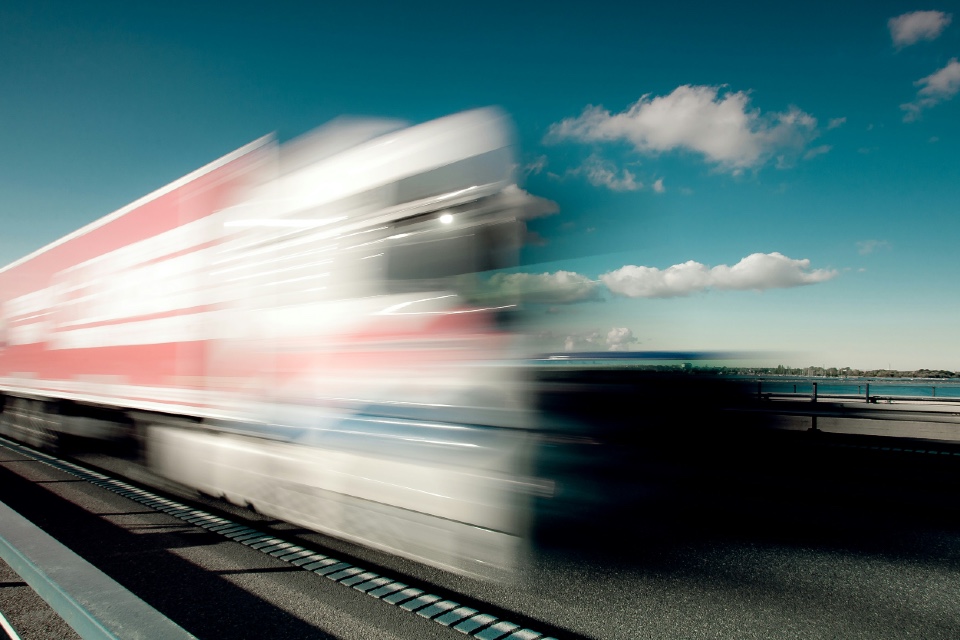
By Serge Schamschula, Head of Ecosystem at Transporeon, A Trimble Company It is fair to say that the EU has certainly been in full ‘green mode’ in recent years, with the aim to reduce net greenhouse gas emissions by at least 55% by 2030. And, in its bid to meet this ambitious, long-term environmental and […]
Why Europe’s driver shortage isn’t just a personnel problem
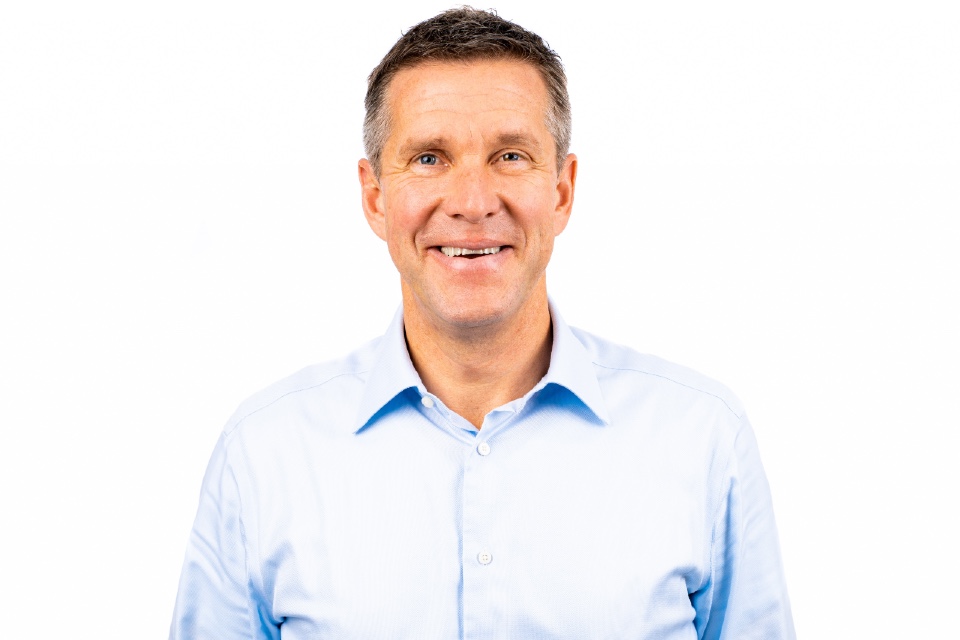
By Stephan Sieber, CEO, Transporeon It’s no secret that global supply chain disruption has dominated headlines since mid-2020. And, over the past three years, the continuing aftershocks of the COVID pandemic, combined with geopolitical factors and an economic downturn, have caused significant upheaval for shippers, cargo receivers, service providers, brokers, freight forwarders, carriers – and […]
How retail fleet managers can improve sustainability and profitability in home delivery
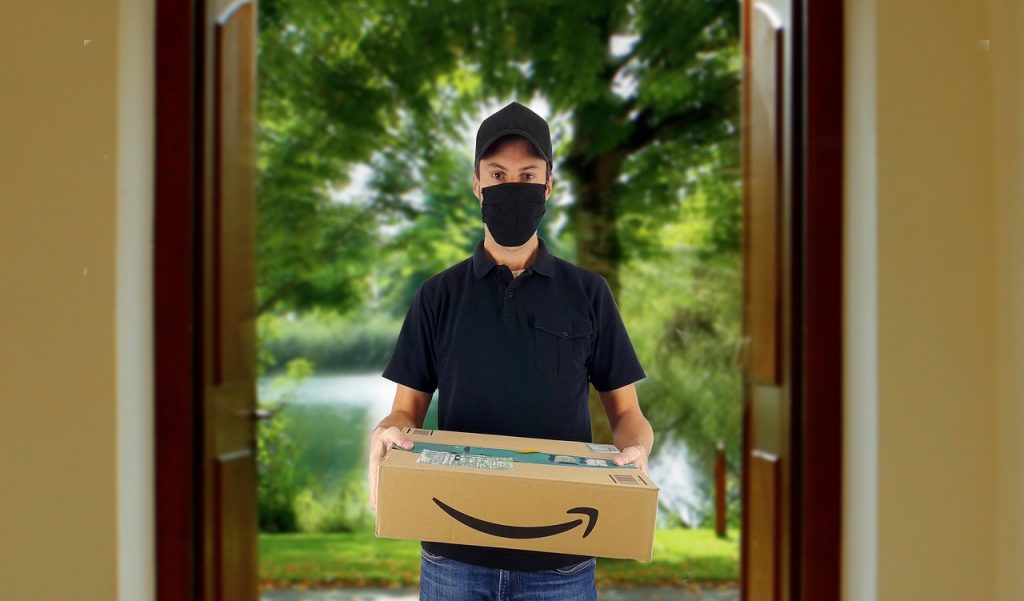
Today, home delivery and sustainability are coming together in consumers’ minds. Descartes recently conducted a comprehensive study to help retailers understand not only how this convergence is changing consumer home delivery preferences; but also how retailers can take advantage of these evolving preferences to help themselves and the environment. The good news is that consumers […]
HGV driver the most in-demand role in transport and logistics
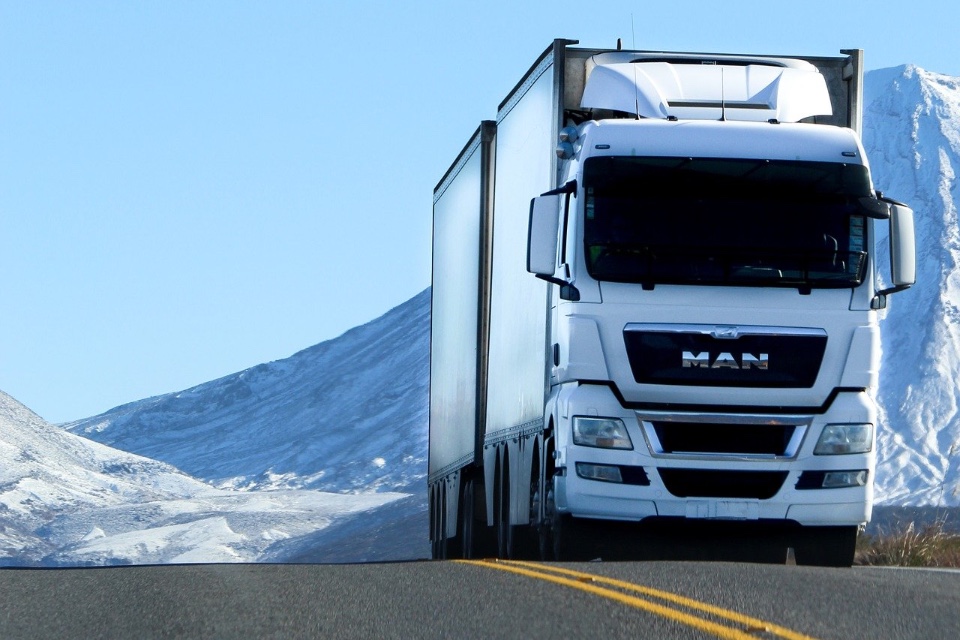
HGV driver and supply chain manager roles are most the most in-demand jobs in logistics, with a respective 7,200 and 4,831 available job postings. At the end of September, there were 52,000 vacancies within the industry as a whole, analysis of Reed & Total Jobs vacancy postings and Road Haulage Association data carried out by […]